Die-cutting is a innovative technique that intricately shapes components into custom designs with finesse and efficiency. Whether you’re producing PCB Shielding Gaskets or Thermal Gap Pads, choosing the right die-cutting equipment can greatly influence the finished product's quality and the smooth operation of your production line. This guide will guide you through critical factors to evaluate, guaranteeing you invest in a system that meets your industry-specific needs while boosting productivity.
Understanding Die-Cutting Technologies and Their Applications
Die-cutting technology has revolutionized numerous industries by offering tailored Die-cutting Solutions that accommodate unique manufacturing requirements. From the creation of Silicone Rubber Gaskets in automotive sectors to Die-cutting EMI Foam for electronic devices, determining the correct type of die-cutting machine is essential. Other niche applications include Die-cutting Mylar Film, which is important in packaging and insulation, and Foil Heat Shield cutting for thermal management solutions.
For applications requiring strong conductivity, like in electric vehicles or electronic casings, utilizing machines capable of Die-cutting Conductive Foam guarantees components such as Die-Cut Solutions for Electric Vehicle Batteries are precisely produced complying with stringent standards.
Key Factors to Evaluate When Choosing Die-Cutting Equipment
1. Material Compatibility: Confirm the die-cutting technology you choose can accommodate specific materials required in your production. For instance, the accurate cutting of Thermal Gap Pads requires equipment suitable for handling its distinct properties without degrading material integrity.
2. Precision and Complexity: High-end die-cutting offers remarkable accuracy — a critical factor when producing complex components like PCB Shielding Gaskets. Evaluate the machine's capacity to perform precise cuts, which is essential for maintaining functionality and fit especially in compact assemblies.
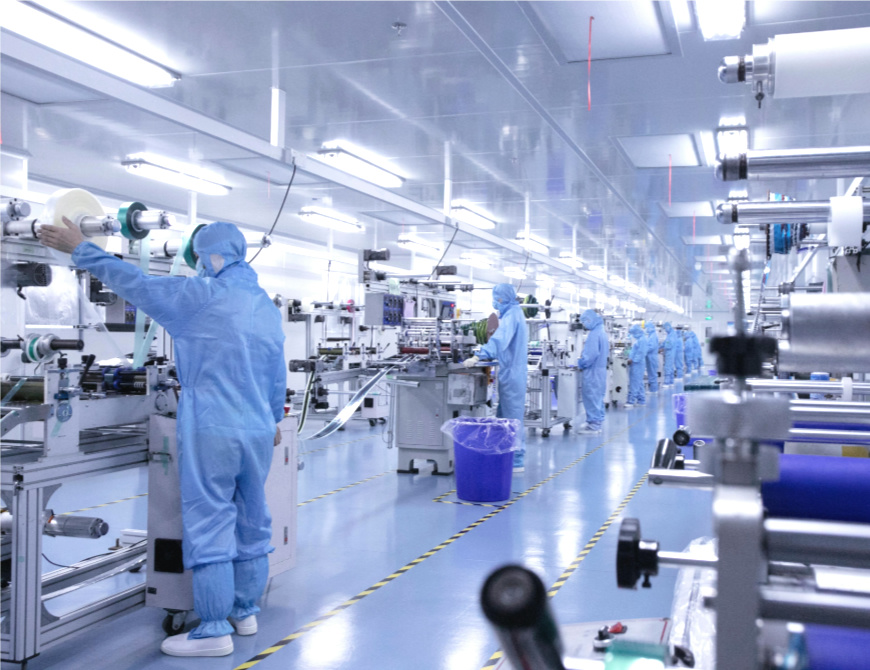
3. Production Volume Capacity: Based on your operational needs, assess whether single-stroke or rotary die equipment is more suitable. Single-stroke machines are generally chosen for lower-volume, high-precision tasks while rotary dies excel for high-volume production runs commonly seen in Automotive Die Cutting.
4. Customization and Flexibility: Trusted providers of Die-cutting Solutions supply businesses with customizable machines that integrate easily to varied production demands. This flexibility permits manufacturers to switch between making Silicone Rubber Gaskets and Foil Heat Shield components without lengthy downtime, improving overall efficiency.
Long-term Dependability and Support
Investing in top-grade die-cutting equipment means evaluating beyond the upfront cost. The endurance of the machine, efficiency of maintenance, availability of spare parts, and technical support are essential in the ongoing functionality and performance of your die-cutting operations. Partner with vendors known for their robust after-sales service who facilitate training sessions to ensure your team fully capitalizes on the technology employed.
Moreover, sustainability aspects cannot be ignored. With energy-efficient designs now available, companies can shrink their environmental footprint while also trimming operational costs associated with power consumption.
Adopting the right die-cutting equipment is instrumental in shaping products with high precision while accelerating production processes across various industries. By targeting compatibility with specific materials, ensuring technological precision for complex designs, and considering adjustable features for diverse manufacturing needs, businesses can realize outstanding productivity and quality enhancements. Such strategic investments not only enhance immediate operational successes but also pave the way for long-term innovation and growth in competitive markets. Embracing these advanced cutting solutions enables companies to stay ahead in delivering specialty products like Electric Vehicle Batteries’ components seamlessly and efficiently.
To learn more about for more details visit this webpage