In a world driven by precision and efficiency, the role of advanced manufacturing techniques like die-cutting cannot be minimized. Die-cutting, a technique known for its fine accuracy and multifunctionality, is reshaping numerous industries by enabling the creation of intricately shaped components with speed and exactitude. This transformative method extends its advantages across various sectors, fostering advancement and enhancing the functionality of countless solutions.
Driving Automotive Excellence with Precision Die-Cuts
The automotive industry greatly profits from precise die-cut technologies. Specifically, automotive die cutting aids in fabricating parts that align perfectly to the complex assemblies of modern cars. By employing state-of-the-art die-cutting technologies, manufacturers guarantee tighter seals with Silicone Rubber Gaskets and better heat distribution with foil heat shields. The benefit is not only superior vehicle performance but also an improvement in manufacturing capacity.
Electrifying Innovations in Electric Vehicles
Die-cut solutions are critical in the progression of electric vehicle systems, primarily through the implementation of components such as Die-Cut Solutions for Electric Vehicle Batteries. These accurately engineered parts help optimize battery storage capacity and enhance the overall reliability and lifespan of the power systems. By minimizing the risk of electrical issues and boosting thermal dissipation, precision die-cuts provide significantly to the sturdiness and dependability of electric vehicles.
Harnessing Superiority in Electronics with Die-Cut Components
In the tech sector, maintaining component integrity and ensuring electromagnetic resistance are crucial. Precision die-cutting fulfills these needs successfully; products like PCB Shielding Gaskets and Die-cutting Conductive Foam are indispensable for protecting delicate electronic components against electromagnetic interference. Furthermore, Die-cutting EMI Foam plays a critical role in preserving the operation of electronic devices by ensuring that they comply with stringent industry requirements.
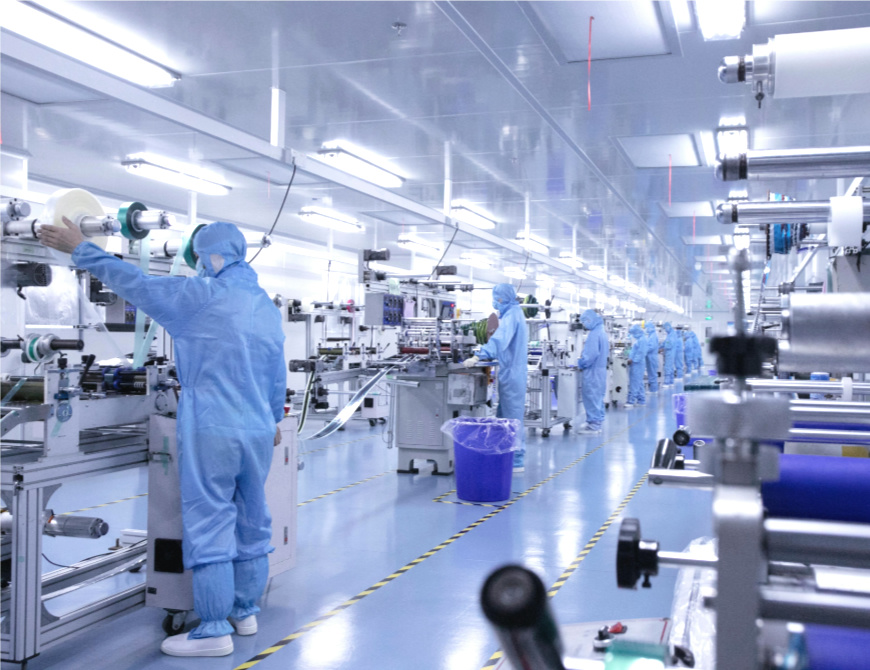
Die-cut Mylar Film, a product of high-precision die-cutting processes, is another example showing how tailored components elevate product design and application in electronics manufacturing. The film acts as a consistent insulator and protective membrane, integral in prolonging the life and performance of electronic devices.
Enhancing Industrial Applications with Thermal and Mechanical Solutions
Industries dealing with thermal regulation rely heavily on advancements provided by die-cutting technologies. Thermal Gap Pads, crafted via precision die-cutting, offer an effective solution for managing heat in space-limited electronic assemblies, thereby increasing system stability and performance. The precision with which these pads are cut ensures that they fit seamlessly into complex structures without compromising on their heat-conductive attributes.
Similarly, in mechanical applications, Silicone Rubber Gaskets made through precision die-cutting processes offer improved sealing solutions that withstand harsh settings while providing longevity and stability—traits that are crucial in industrial settings.
The significant effect of precision die-cutting on industry innovation is evident across a extensive spectrum of deployments—from automotive efficiencies to pivotal enhancements in the operational integrity of electronic systems. By allowing for the manufacture of complex, customized components such as Silicone Rubber Gaskets, PCB Shielding Gaskets, and other specialized items, this technology pushes the boundaries of what's possible in modern engineering. As industries continue to progress towards more sophisticated and high-performance outputs, the role of precision die-cutting stands out as both a facilitator and a catalyst of innovative advancements. Through continual enhancements in die-cutting techniques and materials, the promise for even greater contributions to industrial efficiency and product functionality looks not only likely but inevitable.
For details about more info check our new webpage: look at this now